Processes & Technology
Processes & Technology
BrightChem provides the most advanced green chemical energy solutions, including ammonia, methanol, green ammonia, urea, and more. The company continues to invest in the construction of integrated and intelligent ammonia (methanol) synthesis plants. After years of persistent effort and development, BrightChem is now a leader in the industry.
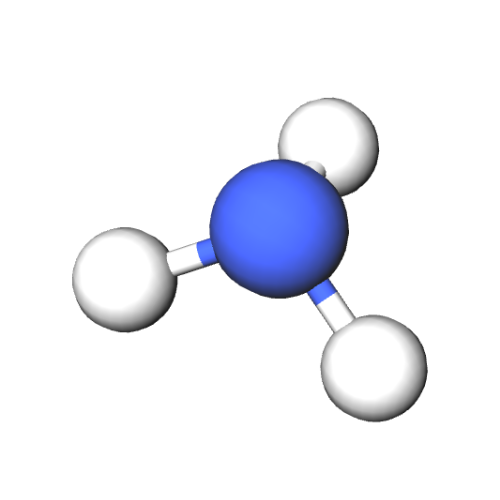
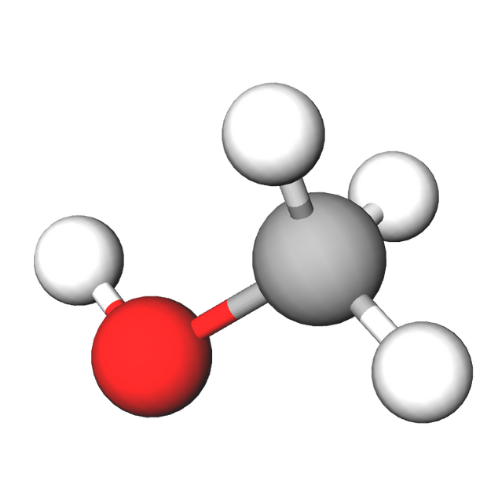
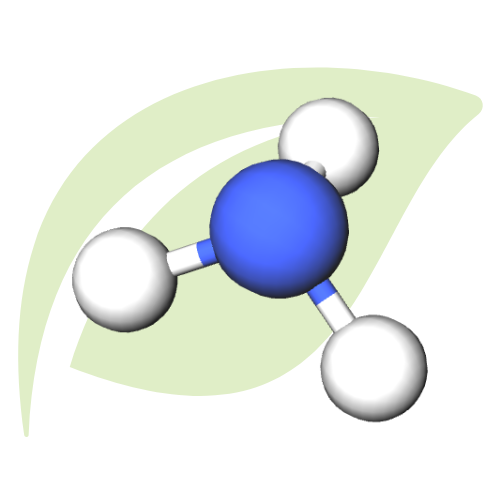
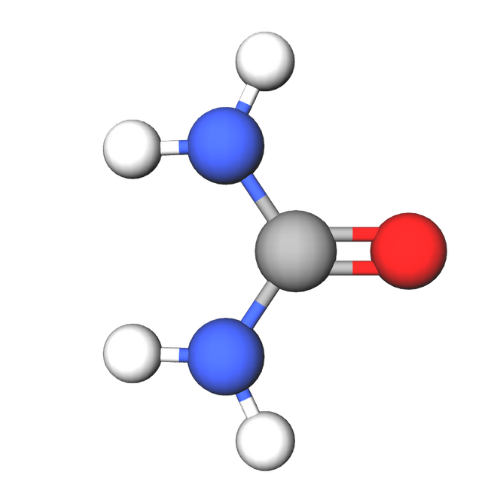
Ammonia Synthesis Process Technology
This process utilizes a high-efficiency ammonia synthesis reactor (zero-meter gas swirl mixer + fish scale plate radial distributor + unequal diameter orifice distributor + new baffle heat exchanger), direct-connected waste heat recovery or heat exchange technology. It innovatively introduces a full-radial large-scale low-pressure GC-type ammonia synthesis reactor and process technology.
Methanol Synthesis Reaction Process Technology
The process utilizes independently developed high-efficiency water-cooled reactors, water-cooled plate reactors, and gas-cooled reactors to achieve process flow, reaction mechanisms, and thermal energy recovery coupling. This results in high methanol purity, a large amount of by-product steam, and high-quality steam.
Green Ammonia Synthesis Reaction Process Technology
The system and method for ammonia synthesis utilizing renewable energy are independently developed. This approach makes full use of green hydrogen and green nitrogen produced from renewable energy sources such as wind and solar power to synthesize green ammonia. The production process of the facility flexibly matches the variability of renewable energy, enabling efficient production of green ammonia products.
Urea Plant Process Technology
We provide the most mature solutions for constructing modern, intelligent urea plants. Our urea plants utilize the most established ammonia stripping technology. One of the key design principles followed by our team is to deliver a highly automated green urea facility for our clients. In addition to the necessary engineers in the central control room, no additional operators are required. The control system’s HMI has been optimized based on the continuous efforts and research of the Capso engineering team.